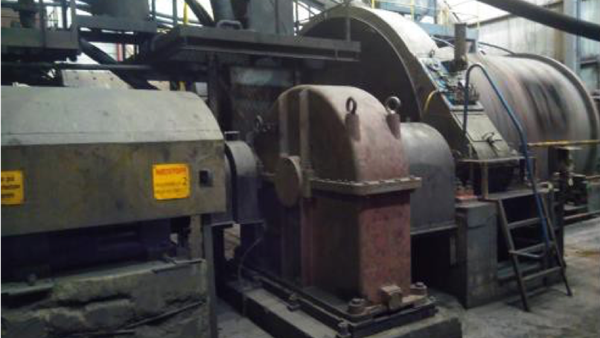
Major savings through route-based condition monitoring on ball mill
Using the handheld instrument Leonova Emerald and DuoTech accelerometers, Norwegian mining company Rana Gruber monitors the mechanical condition of the production-critical ball mill in this case study. The planned replacement of a damaged main bearing, detected through route-based measurement, saved the company significant amounts.
Ball mills are a low-speed application (typical rotational speed is 10-20 RPM), where bearing damage can be challenging to detect. Condition monitoring of the ball mill began in December 2016 and right from the start, the readings indicated potential damage on the output main bearing.
As the months passed, the readings remained at a fairly high but stable level, while the BPFO values showed an increasing trend and clear BPFO matches. When the bearing was replaced during a planned maintenance stop, outer race damage was confirmed.
Download full case study
Case Study
CS021 - Ball mill - Rana GruberFilename/description | Language | Size | Modified | |
---|---|---|---|---|
CS_021B_Ball_mill_RanaGruber_NO.pdf | English (United Kingdom) | 910 kB | 11/8/2018 | |
This case study describes the detection of bearing damage on one of the main bearings in a 60 ton ball mill. |